Porosity in Welding: Identifying Common Issues and Implementing Best Practices for Prevention
Porosity in welding is a prevalent problem that often goes undetected up until it triggers considerable troubles with the integrity of welds. In this discussion, we will certainly explore the essential variables adding to porosity formation, examine its damaging impacts on weld efficiency, and review the finest methods that can be embraced to decrease porosity occurrence in welding procedures.
Typical Root Causes Of Porosity

Utilizing unclean or damp filler products can present pollutants into the weld, adding to porosity problems. To mitigate these typical reasons of porosity, detailed cleansing of base metals, correct shielding gas option, and adherence to ideal welding specifications are crucial practices in attaining high-grade, porosity-free welds.
Effect of Porosity on Weld High Quality

The presence of porosity in welding can dramatically jeopardize the structural integrity and mechanical residential properties of bonded joints. Porosity produces gaps within the weld metal, weakening its general strength and load-bearing ability.
One of the key repercussions of porosity is a reduction in the weld's ductility and strength. Welds with high porosity degrees tend to show reduced influence stamina and lowered ability to deform plastically before fracturing. This can be especially concerning in applications where the bonded components are subjected to dynamic or cyclic loading problems. Porosity can hamper the weld's capacity to efficiently transfer pressures, leading to premature weld failing and possible safety dangers in critical structures. What is Porosity.
Ideal Practices for Porosity Prevention
To improve the architectural integrity and high quality of welded joints, what specific steps can be implemented to lessen the event of porosity during the welding procedure? Porosity avoidance in welding is vital to ensure the integrity and toughness of the last weld. One reliable method appertains cleansing of the base steel, eliminating any type of contaminants such as rust, oil, paint, or wetness that might result in gas entrapment. Making sure that the welding tools remains in good problem, with tidy consumables and appropriate gas circulation rates, can additionally dramatically minimize porosity. Additionally, maintaining a steady arc and managing the welding specifications, such as voltage, current, and about his take a trip speed, aids produce a consistent weld pool that reduces the danger of gas entrapment. Utilizing the appropriate welding technique for the details product being welded, such as readjusting the welding angle and weapon setting, can further protect against porosity. Regular evaluation of welds and immediate remediation of any concerns recognized during the welding procedure are crucial practices to avoid porosity and generate premium welds.
Importance of Proper Welding Strategies
Applying correct welding methods is extremely important in guaranteeing the structural stability and high quality of welded joints, building on the foundation of reliable porosity prevention steps. Welding techniques straight influence the total stamina and sturdiness of the welded structure. One vital facet of appropriate welding strategies is maintaining the proper warm input. Extreme warm can lead to boosted porosity due to the entrapment of gases in the weld swimming pool. Conversely, not enough warm might lead to insufficient blend, creating prospective powerlessness in the joint. Additionally, making use of the appropriate welding specifications, such as voltage, existing, and travel rate, is essential for achieving audio welds with minimal porosity.
Additionally, the choice of welding process, whether it be MIG, TIG, or stick welding, need to align with the specific needs of the project to make certain optimal outcomes. Proper cleansing and preparation of the base steel, along with choosing the ideal filler material, are likewise vital parts of skillful welding strategies. By adhering to these best techniques, welders can minimize the threat of porosity formation and produce high-grade, structurally audio welds.
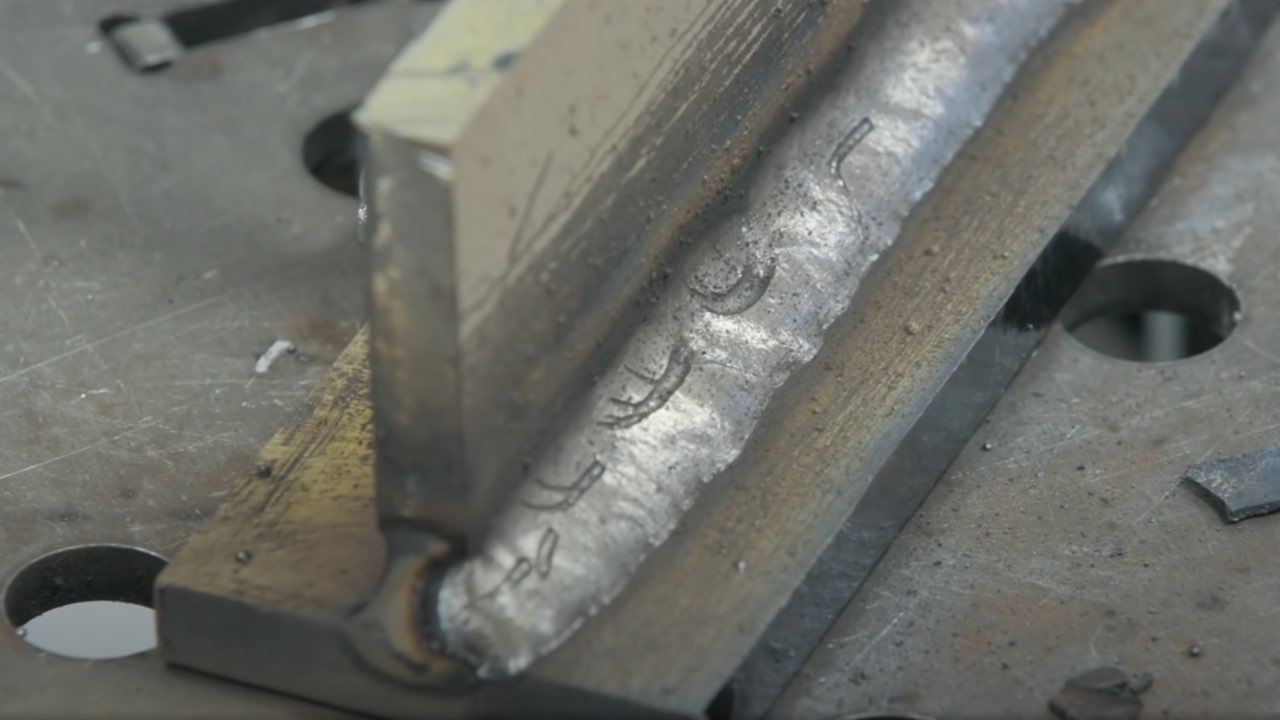
Examining and Quality Assurance Procedures
Quality assurance procedures play an important role in verifying the honesty and reliability of welded joints. Examining procedures are necessary to spot and protect against porosity in welding, ensuring the toughness and durability of the end product. Non-destructive screening techniques such as ultrasonic testing, radiographic screening, and aesthetic assessment are frequently employed to determine possible problems like porosity. These strategies enable the evaluation of weld top quality without compromising the honesty of the joint. What is Porosity.
Post-weld assessments, on the other hand, assess the final weld for any kind of problems, consisting of porosity, and verify that it fulfills specified criteria. Executing an extensive top quality control plan Full Article that includes complete screening procedures and inspections is critical to minimizing porosity concerns and ensuring the general high quality of bonded joints.
Verdict
To conclude, porosity in welding can be a typical problem that influences the top quality of welds. By identifying the usual sources of porosity and applying best practices for prevention, such as proper welding methods and testing procedures, welders like this can make certain excellent quality and reliable welds. It is vital to prioritize prevention techniques to lessen the incident of porosity and preserve the honesty of bonded frameworks.